Monitoring and Control Techniques in Construction Projects: Ensuring Project Success
Effective monitoring and control are integral to the success of construction projects. These techniques help project managers track progress, identify deviations, and implement corrective actions to ensure that projects remain aligned with their objectives. This blog explores key monitoring and control methods, including schedule control, cost variance analysis, quality metrics, and performance measurement baselines, while highlighting their importance in delivering successful construction projects.
Table of Contents
The Importance of Monitoring and Control
Monitoring and control involve systematically observing project activities, comparing actual performance against planned baselines, and making adjustments as necessary. These processes are essential for:
- Ensuring Progress Alignment: Tracking milestones ensures that the project stays on schedule.
- Maintaining Budget Compliance: Monitoring costs prevents overspending and identifies potential savings.
- Enhancing Quality Standards: Regular inspections ensure deliverables meet specifications.
- Mitigating Risks: Early detection of issues allows for timely corrective actions.
Monitoring and Control Framework
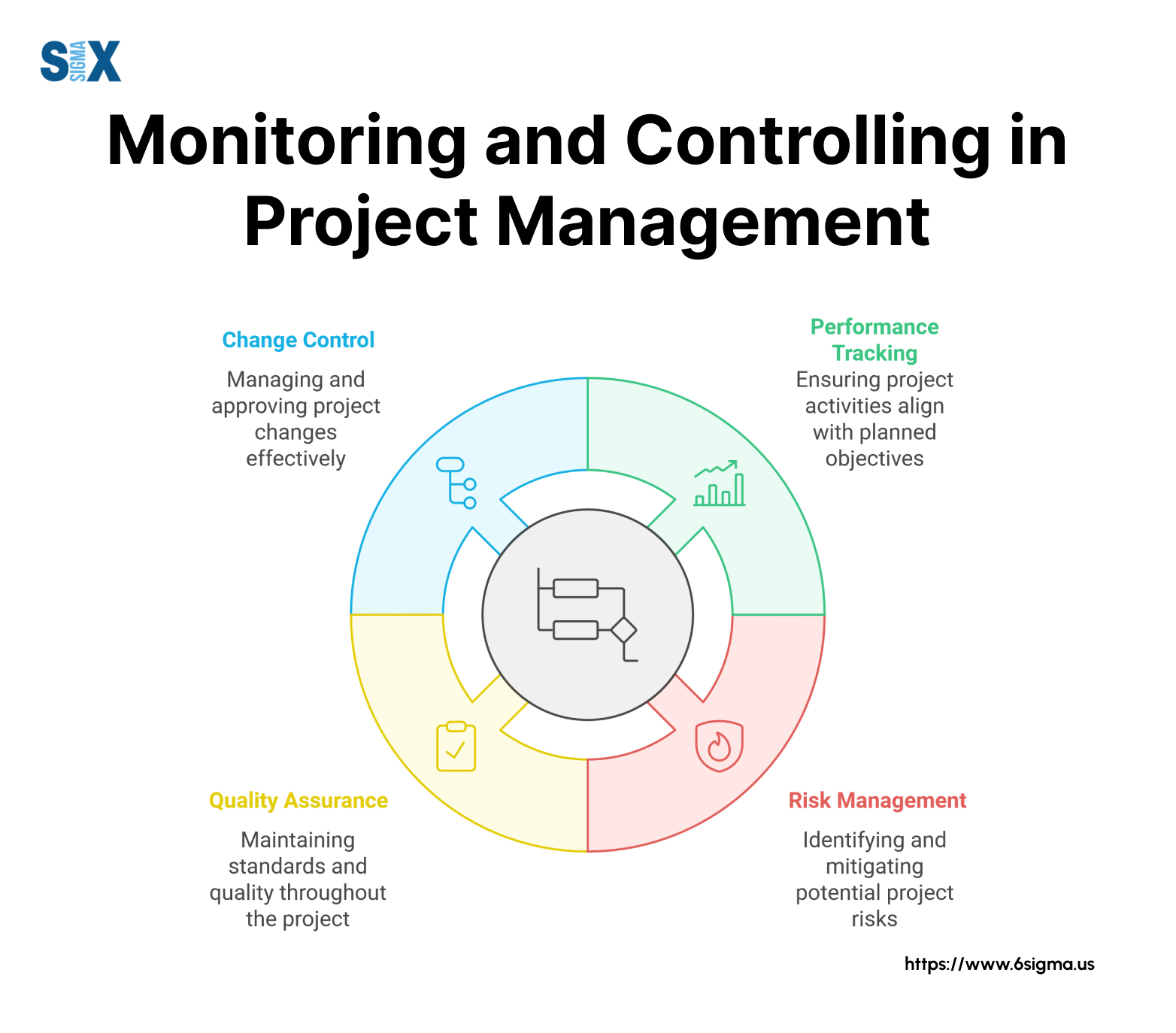
Figure 1: Key components of construction project monitoring and control
Key Monitoring Techniques
1. Schedule Control
Schedule control ensures that project timelines are adhered to by tracking progress against planned schedules and identifying delays early.
Techniques for Schedule Control:
- Critical Path Method (CPM): Identifies the sequence of tasks that directly impact the project timeline.
- Earned Value Management (EVM): Combines schedule performance with cost metrics to assess progress.
- Progress Tracking Tools: Software like Primavera P6 or Microsoft Project provides real-time updates on task completion.
Example:
In a bridge construction project:
- CPM analysis revealed delays in foundation work.
- Additional crews were deployed to recover lost time without affecting subsequent activities.
2. Cost Variance Analysis
Cost variance analysis compares actual expenditures with budgeted costs to identify discrepancies and manage financial risks.
Metrics Used in Cost Variance Analysis:
- Planned Value (PV): Budgeted cost for scheduled work.
- Earned Value (EV): Budgeted cost for completed work.
- Actual Cost (AC): Actual expenditure incurred.
Example:
For a residential housing project:
- PV = ₹30 lakh; EV = ₹25 lakh; AC = ₹28 lakh.
- Cost Performance Index (CPI) = EV ÷ AC = ₹25 lakh ÷ ₹28 lakh = 0.89 (indicating overspending).
Corrective actions included renegotiating supplier contracts to reduce material costs.
3. Quality Metrics
Quality metrics ensure that construction deliverables meet specified standards through systematic inspections, testing protocols, and non-conformance management.
Common Quality Metrics:
- Defect Rate: Measures the frequency of defects per unit area or volume.
- Compliance Rate: Tracks adherence to regulatory standards.
- Inspection Pass Rate: Percentage of inspections passed without rework.
Example:
In a high-rise building project:
- Daily inspections revealed non-compliance in concrete strength tests.
- Corrective actions included re-pouring affected sections using higher-grade concrete.
4. Performance Measurement Baselines
Performance measurement baselines provide reference points for evaluating project progress across scope, schedule, cost, and quality dimensions.
Components of Performance Baselines:
- Scope Baseline: Defines deliverables and exclusions.
- Schedule Baseline: Establishes timelines for milestones.
- Cost Baseline: Sets budget allocations for activities.
- Quality Baseline: Specifies standards for materials and workmanship.
Performance Measurement Dashboard

Figure 2: Sample dashboard showing performance metrics across scope, schedule, cost, and quality
Tools for Effective Monitoring and Control
Modern construction projects leverage technology to enhance monitoring and control processes:
1. Project Management Software
Tools like Procore or Primavera P6 centralize project information, streamline communication, and provide real-time updates on progress.
2. Building Information Modeling (BIM)
BIM enables virtual inspections, clash detection, and progress visualization through 3D models.
3. Drones and IoT Sensors
Drones provide aerial views for site monitoring, while IoT sensors track equipment usage, environmental conditions, and structural integrity.
Practical Application in Construction Projects
Case Study: Commercial Office Complex
Scenario:
A commercial office complex faced challenges with schedule delays due to resource shortages and quality issues in interior finishes.
Solution:
The contractor implemented integrated monitoring and control techniques:
- Schedule Control:
- Used CPM analysis to identify delayed activities.
- Deployed additional labor for interior finishing tasks.
- Used CPM analysis to identify delayed activities.
- Cost Variance Analysis:
- Conducted weekly reviews of budget compliance using EVM metrics.
- Negotiated discounts with suppliers to offset increased labor costs.
- Conducted weekly reviews of budget compliance using EVM metrics.
- Quality Metrics:
- Conducted daily inspections using digital checklists linked to BIM models.
- Addressed non-conformance issues through root cause analysis.
- Conducted daily inspections using digital checklists linked to BIM models.
- Performance Baselines:
- Updated scope baseline after stakeholder approval of design changes.
- Revised schedule baseline to reflect accelerated timelines.
- Updated scope baseline after stakeholder approval of design changes.
Results:
- Reduced overall project duration by three weeks.
- Achieved compliance with quality standards across all phases.
- Delivered the project within budget despite initial variances.
Challenges in Monitoring and Control
Despite their benefits, implementing effective monitoring and control techniques can be challenging:
Common Issues:
- Data Overload: Managing large volumes of information from multiple sources can be overwhelming.
- Resistance to Technology Adoption: Teams may resist using advanced tools due to unfamiliarity or perceived complexity.
- Communication Gaps: Poor coordination among stakeholders can hinder decision-making.
- Resource Constraints: Limited access to skilled personnel or technologies can impact effectiveness.
Solutions:
- Use user-friendly software tools with intuitive interfaces.
- Provide training sessions to familiarize teams with new systems.
- Establish clear communication protocols across all project levels.
- Allocate dedicated resources for monitoring tasks.
Conclusion
Monitoring and control are indispensable processes in construction project management that ensure projects remain aligned with their objectives while minimizing risks associated with delays, cost overruns, or quality issues.
By implementing structured techniques such as schedule control methods, cost variance analysis, quality metrics evaluation, and performance measurement baselines—construction managers can enhance project outcomes significantly.
Additional Reads:
Scope Verification and Control in Construction